Hypersonic vehicles must be able to send and receive information while operating at the high temperatures associated with speeds of Mach 5 (five times the speed of sound) or greater. To support development of these vehicles, the Georgia Tech Research Institute (GTRI) is testing the ability of specialized low-loss materials to transmit electromagnetic signals at temperatures measured in thousands of degrees Celsius.
Using GTRI’s free-space focused-beam electromagnetic test system, the research is providing new information about the intrinsic properties of low-loss materials at such high temperatures, not only helping facilitate the design of hypersonic vehicles, but also providing data that could lead to development of improved electromagnetic window materials.
“There is an entire class of materials that must be able to meet requirements for mechanically surviving speed, pressure, and temperature while propagating electromagnetic energy,” said GTRI Research Engineer Christopher Howard. “We can accurately validate the properties of the materials being developed with these applications in mind, and also provide information that can go into computational electromagnetic modeling to create even better materials.”
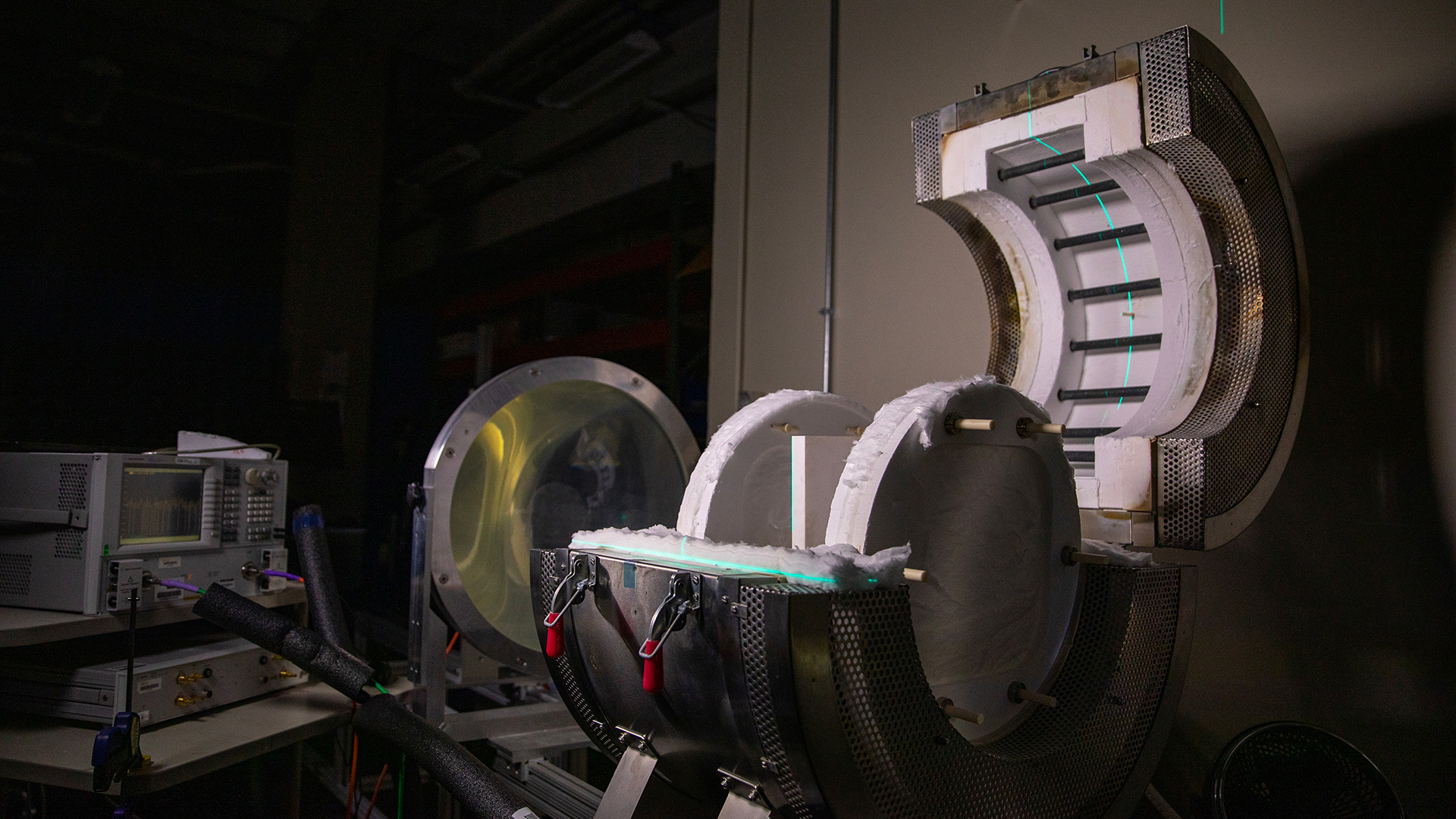
GTRI researchers are using this tube furnace to measure the ability of specialized low-loss materials to transmit electromagnetic signals at temperatures measured in thousands of degrees Celsius. Photo credit: Sean McNeil.
How Measurements are Made
Intended for use in radomes and antenna apertures, the materials are evaluated in a furnace with custom-fabricated windows designed to let electromagnetic signals pass through, allowing the properties of the materials to be measured. The equipment first uses a large dielectric lens to focus the energy from a transmit feed onto the sample within the furnace, which can be operated at up to 1,200 degrees Celsius (nearly 2,200 degrees Fahrenheit). A second identical lens captures the signals after they pass through the furnace and the material under test, allowing GTRI-developed software to then analyze how the material affects beam transmission.
So far, the work has produced data on more than 20 different samples provided by federal government agencies. Supported by the Air Force Research Laboratory and Georgia Tech’s participation in the University Consortium for Applied Hypersonics (UCAH), the research can evaluate transmission of millimeter-wave and microwave signals with high accuracy and the ability to measure even small amounts of loss.
Video: GTRI high-temp electromagnetic testing overview.
“The challenge of doing these measurements is that antennas and network analyzers can’t be taken into test chambers at those temperatures,” said Taylor Shapero, a GTRI research scientist who developed improvements to the furnace. “To study electromagnetic energy propagating through the sample, we created windows that are transparent to the electromagnetic energy, yet are good thermal insulators that allow us to transmit through the furnace to collect information about how the waves change as a function of the test materials interfering with the beam.”
Samples evaluated in the equipment vary by size according to the wavelengths to be measured. For instance, broadband measurements can be done with samples up to 12 inches or larger. But studies of specific narrow wavelengths – and evaluations of small differences in loss properties – are done on samples the size of a toothpick.
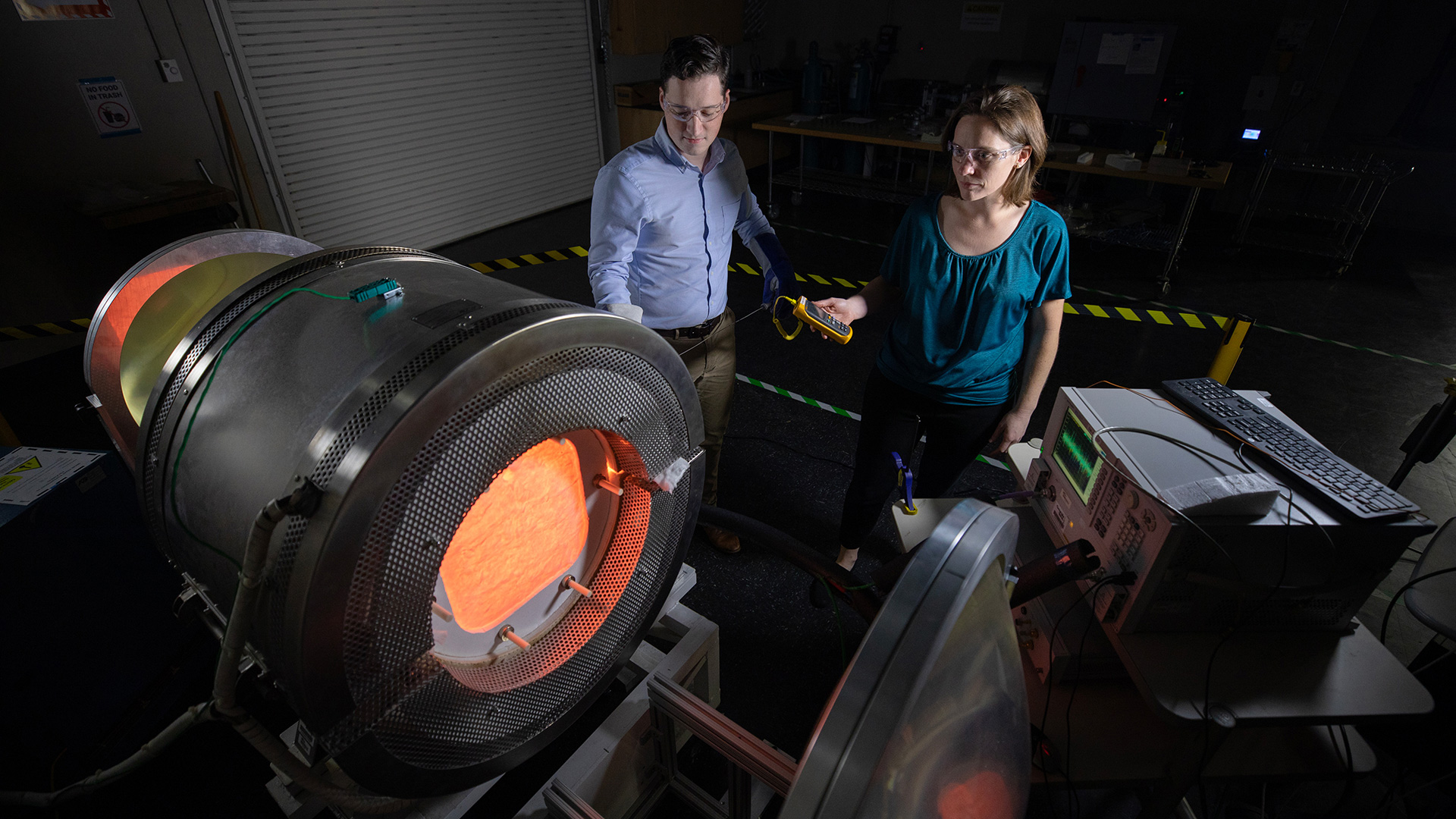
Researchers Christopher Howard and Taylor Shapero verify the temperature of a furnace used to measure the ability of specialized low-loss materials to transmit electromagnetic signals at high temperatures. The furnace can reach temperatures of 1,200 degrees C. Photo credit: Sean McNeil.
Not surprisingly, the testing has involved mostly ceramic materials, but also some fluoropolymers and circuit board materials. GTRI’s research on evaluating materials for radomes and antenna apertures goes back decades, but the interest in materials for use in hypersonic vehicles has grown in recent years – and required adjustments in measurement approaches.
“There are unique challenges associated with hypersonic speeds,” said David Reid, a GTRI principal research engineer. “The extreme heat and extreme speeds mean the materials we’ve been using for decades won’t work anymore. This has now become a national priority, and we have developed techniques to measure materials in this very challenging environment.”
Improving Techniques for Studying Hypersonic Materials
Expanding high-temperature electromagnetic transmission required improvements in GTRI’s tube furnace to ensure consistent temperatures of the samples and prevent expansion and contraction of the lenses used to focus the beam as it passes through the samples. Those effects on the lenses could create measurement drift if not controlled.
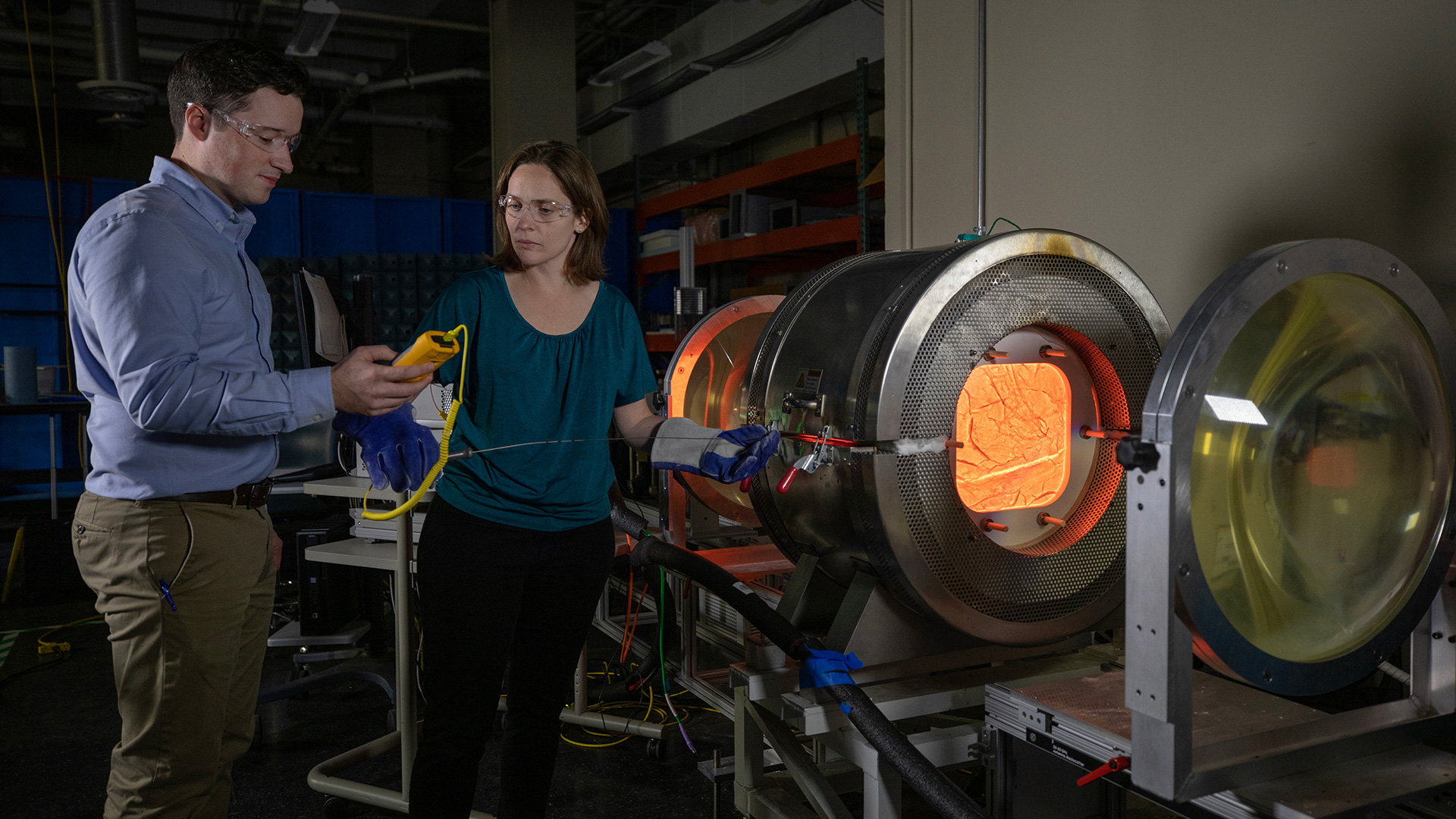
Researchers Christopher Howard and Taylor Shapero verify the temperature of a furnace used to measure the ability of specialized low-loss materials to transmit electromagnetic signals at high temperatures. Photo credit: Sean McNeil.
Researchers replaced the old rigid alumina- and silicon oxide-based windows with two-inch-thick low-density alumina blankets reinforced by an alumina frame. “We wanted a material that had both the thermal and mechanical properties, and also a low density and low loss so we’d be measuring only the sample materials,” Shapero said.
Some of the potential replacements were not rigid enough, while others had a density too high. The researchers ultimately found an appropriate material, and worked with GTRI’s Machine Services Department to design, fabricate and install the new windows. “Taylor carefully probed the temperature within the volume of the furnace and showed that the improvements she designed for the windows gave us a more uniform temperature distribution within the sample holder,” Reid said.
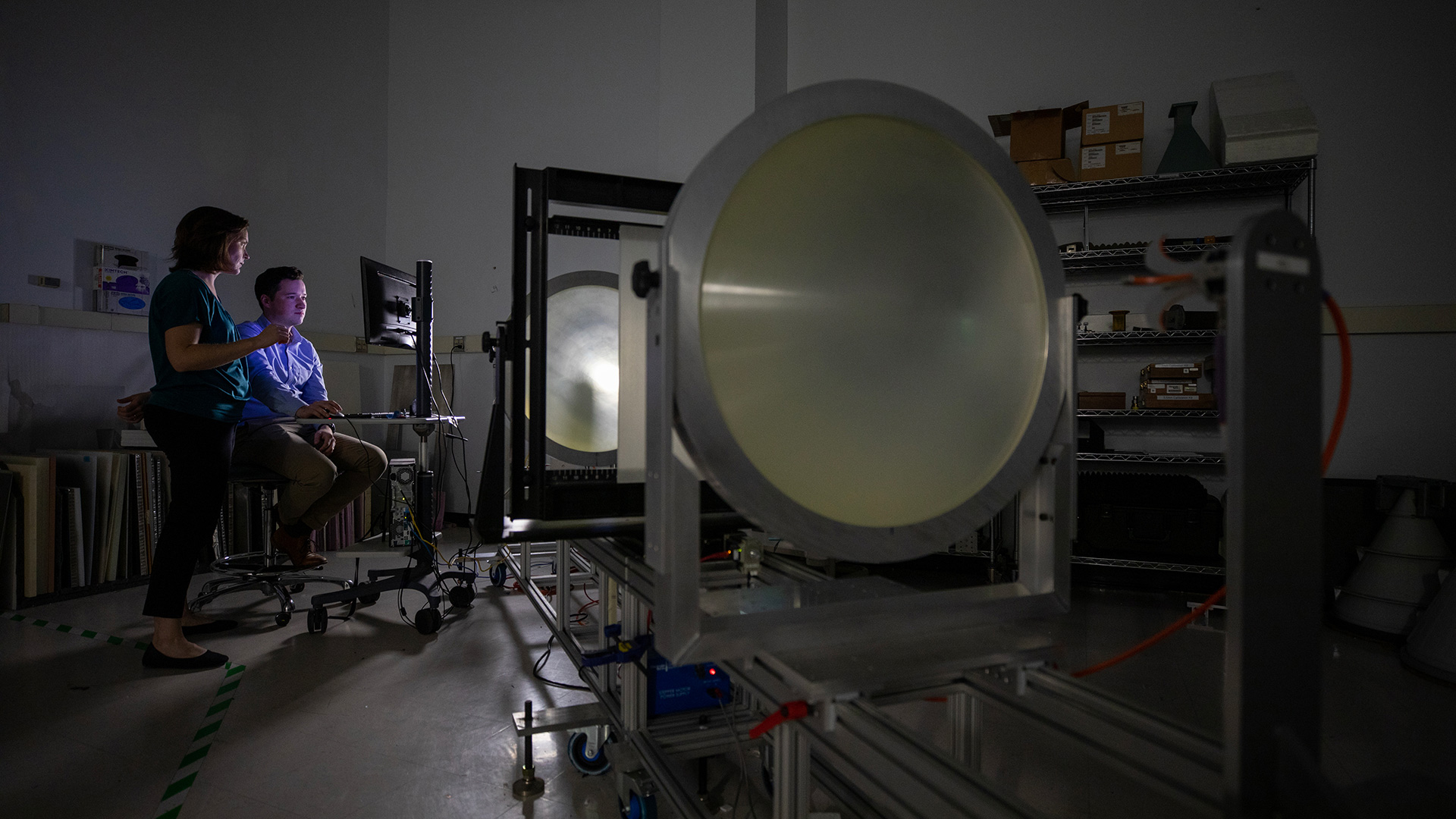
GTRI-developed software analyzes how the high-temperature material affects transmission of electromagnetic signals. Shown are researchers Taylor Shapero and Christopher Howard. Photo credit: Sean McNeil.
Beyond obtaining the data, the researchers also improved their analysis algorithm. “Christopher worked to find each and every potential source of error, looking for ways to improve the quality of the measurement and analysis,” Reid added. “There was lots of detective work to identify and fix any sources of uncertainty.”
While 1,200 degrees Celsius may seem plenty hot, hypersonic vehicles traveling a Mach 10 or more could get much hotter. To evaluate materials under those conditions, GTRI is now working with researchers from Georgia Tech’s School of Mechanical Engineering under UCAH support to develop a furnace able to reach 3,000 degrees Celsius.
Writer: John Toon (john.toon@gtri.gatech.edu)
GTRI Communications
Georgia Tech Research Institute
Atlanta, Georgia USA
MORE 2022 ANNUAL REPORT STORIES
MORE GTRI NEWS STORIES
The Georgia Tech Research Institute (GTRI) is the nonprofit, applied research division of the Georgia Institute of Technology (Georgia Tech). Founded in 1934 as the Engineering Experiment Station, GTRI has grown to more than 2,800 employees supporting eight laboratories in over 20 locations around the country and performing more than $700 million of problem-solving research annually for government and industry. GTRI's renowned researchers combine science, engineering, economics, policy, and technical expertise to solve complex problems for the U.S. federal government, state, and industry.